Modernization Vulnerabilities in Manufacturing Sectors: Cybersecurity Weaknesses Expose Companies to Threats
The looming threat to America's industrial heart is escalating as manufacturers hastily advance toward digitization, seemingly oblivious to the perils. The crux of the issue stems from the inherent disconnect between old-school and modern technologies. Industrial control systems (ICS) and SCADA (Supervisory Control and Data Acquisition) networks were designed as standalone entities, never intended to interface with the internet. Yet, the push for digital transformation now forces these systems online, creating a precarious equilibrium between productivity and security.
We've witnessed the repercussions of this tightrope act firsthand. A Fortune 500 multinational corporation found itself grappling with a catastrophic loophole. In their quest to modernize production facilities, they connected their SCADA network with cloud-based analytics and remote monitoring solutions. However, they inadvertently exposed several SCADA endpoints to the public internet, lacking strong authentication controls or network segmentation. This left these systems susceptible to attackers.
The fallout was critical and far-reaching. Unauthorized access to SCADA systems could potentially control industrial processes, leading to production downtime. Given that these systems manage physical equipment, any breach could endanger workers and potentially damage valuable assets. The sanctity of critical telemetry data was also at stake—attackers could tamper with parameters, resulting in incorrect production output.
Industries often impose stringent cybersecurity regulations for ICS/SCADA, such as NIST 800-82 and IEC 62443. Negligence in cybersecurity could trigger hefty fines and irreparable harm to a company's reputation.
This serves as a wake-up call for an industry barreling toward digital transformation, seemingly unaware of the lurking dangers. The manufacturing sector's fervor for cloud computing and remote monitoring might amplify efficiency, but it's also fostering vulnerabilities in systems that were never designed for internet connections.
The Instant Peril
Consider this: The industrial control systems guiding our factories today were built for an age when physical security was enough—when a locked door and a security guard could safeguard your assets. Now, in our haste to modernize, we're linking these same systems to the internet, often via poorly fortified cloud solutions and remote access tools.
In the aforementioned scenario, attackers could potentially seize control of factory equipment, jeopardizing workers, suspending production, or even worse—all without the company's awareness. Traditional security tools were blind to these vulnerabilities because they couldn't detect them.
It's a sightline that's fast becoming a common issue in manufacturing, where the frontiers between operational technology and information technology are increasingly blurring.
The Blind Spots in Traditional Security
In spite of implementing standard security measures like vulnerability scanners and network monitoring, organizations frequently remain oblivious to their true exposures. Case in point: several prominent manufacturers whose internet-accessible OT assets were found during routine external scans. These weren't merely oversights—they encompassed exposed programmable logic controllers (PLCs), human-machine interfaces (HMIs), and even remote terminal units (RTUs) managing industrial processes. Their internal security teams were blissfully unaware that these systems were accessible via the public internet.
Why do these blind spots persist? The underlying cause often lies in the evolving nature of industrial networks. A vendor might add a cellular modem for remote maintenance, or an engineer might set up a makeshift VPN for remote monitoring that becomes permanent. Traditional security tools miss these exposures because they're based on outdated assumptions—they scour known networks, check registered assets, and monitor documented systems. In today's manufacturing landscapes, where shadow OT and unmanaged connections proliferate, this internal-first approach can create significant gaps in security.
Seeing Your Factory Through an Attacker's Eyes
Industrial networks necessitate a fundamental shift in the way they're monitored and protected. Embracing an "outside-in" approach instead of a traditional "inside-out" one would provide a more effective line of defense. This outside-in approach treats a manufacturer's infrastructure from the perspective of an attacker.
This outside-in approach has demonstrated success in practical scenarios. One prominent manufacturer utilized outside-in reconnaissance to survey its externally exposed systems using OSINT (open-source intelligence) techniques that hackers might deploy to identify the best route into their organization. This exercise pinpointed multiple internet-facing industrial systems that their traditional security tools hadn't detected, including exposed SCADA endpoints controlling vital production processes, industrial protocol converters enabling remote access, and human-machine interfaces (HMIs) with default credentials still enabled.
Action Steps:
Inspect external exposures first and foremost. Since 80% of breaches involve external actors, it makes sense to commence by identifying what's visible from the internet. Look for any internet-facing industrial assets, such as controllers, HMIs, protocol converters, and remote access solutions.
Employ a wide discovery net. Limit security assessments neither to known assets nor to networks. Scan across all business units, subsidiaries, and acquisitions to uncover "shadow OT"—industrial systems connected to the internet without the security team's knowledge.
Thoroughly test. Systematically inspect all discovered assets, not merely critical ones. This should include checking for default credentials, unpatched vulnerabilities, and insecure configurations specific to industrial systems.
Evaluate impact, not merely technical severity. When prioritizing which vulnerabilities to address, consider business impact factors like operational dependencies, safety implications, and regulatory requirements particular to industrial environments.
Integrate findings broadly. Ensure that discovered exposures are communicated to all relevant stakeholders—from security teams to operations personnel to executive leadership—to foster coordinated remediation efforts.
The Hard-Earned Lessons
Some argue that digital transformation's benefits in manufacturing outweigh its risks—and they're correct, provided we prioritize security. Although the scenario I described unfolded fortunately, with vulnerabilities flagged and rectified before a disaster struck, we may not always be so fortunate as the attack surface increases.
Modernization in manufacturing is inevitable, but its success hinges on addressing cybersecurity not just as an IT concern, but as a fundamental operational risk that demands leadership attention. It's high time to act, securing these newly connected systems before attackers exploit them, and we learn these lessons the hard way.
In the rush to digitize the manufacturing sector, a growing concern arises from the integration of outdated SCADA systems with modern technologies, such as cloud-based solutions and remote monitoring tools. This hasty convergence can introduce potentially catastrophic risks, leaving systems vulnerable to unauthenticated attacks and data breaches (cybersecurity).
Manufacturers should address these threats proactively, scrutinizing their externally exposed systems first and foremost, employing a wide discovery net to identify shadow OT, and evaluating impact beyond technical severity (seeing your factory through an attacker's eyes). Industries must also take action to secure programmable logic controllers (PLCs), human-machine interfaces (HMIs), and remote terminal units (RTUs) managing industrial processes, often found to be accessible via the public internet (blind spots in traditional security).
Effective cybersecurity in modern manufacturing requires a fundamental shift in monitoring and protection methods, adopting an "outside-in" approach to treat manufacturing infrastructure as if from the perspective of an attacker (the outside-in approach). Negligence in addressing these risks could lead to hefty fines, irreparable harm to a company's reputation, and even physical danger to workers and valuable assets (consider this).
In an era where the frontiers between operational technology and information technology increasingly blur, it is crucial for manufacturers to maintain a vigilant stance against cyber threats. The stakes are high, and it is better to secure these newly connected systems before attackers exploit the gaps, costing both time and resources in remediation efforts (the hard-earned lessons).
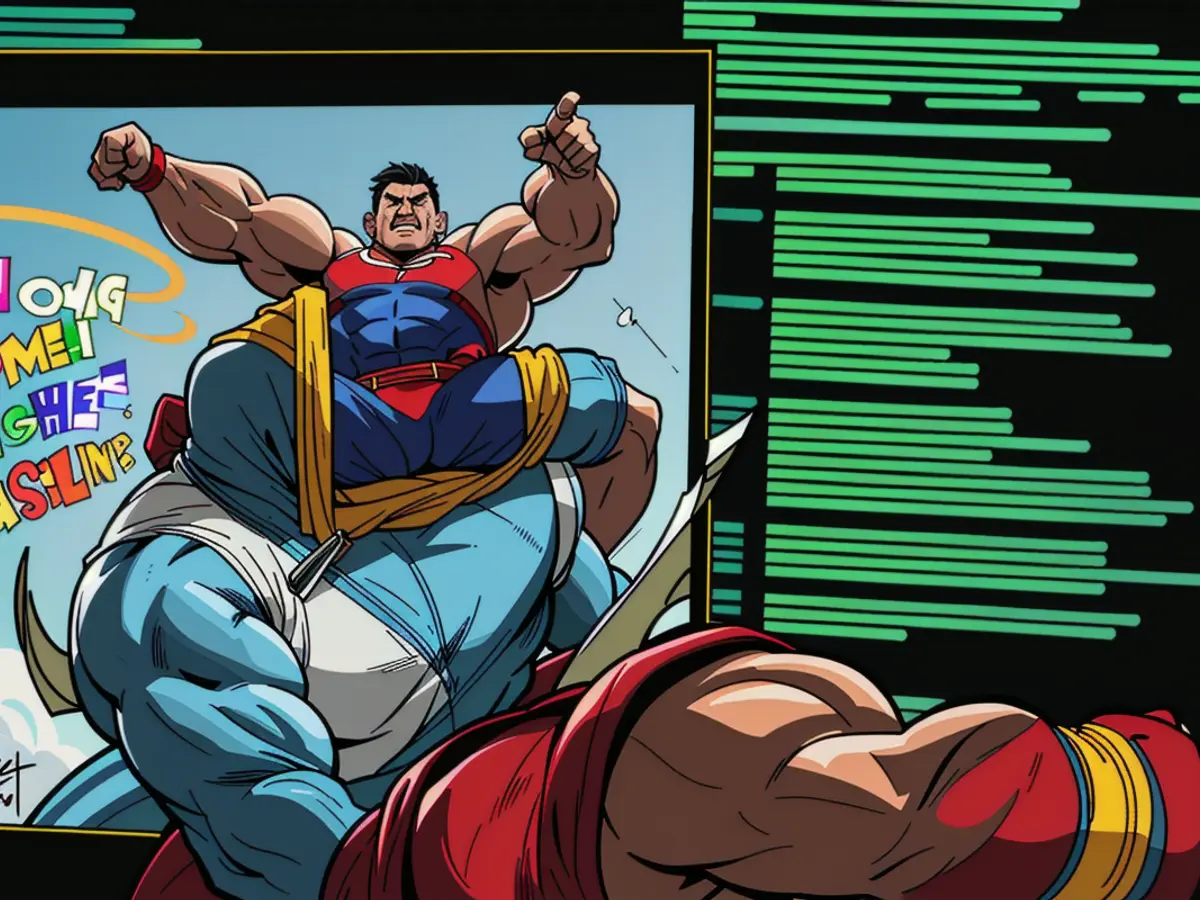
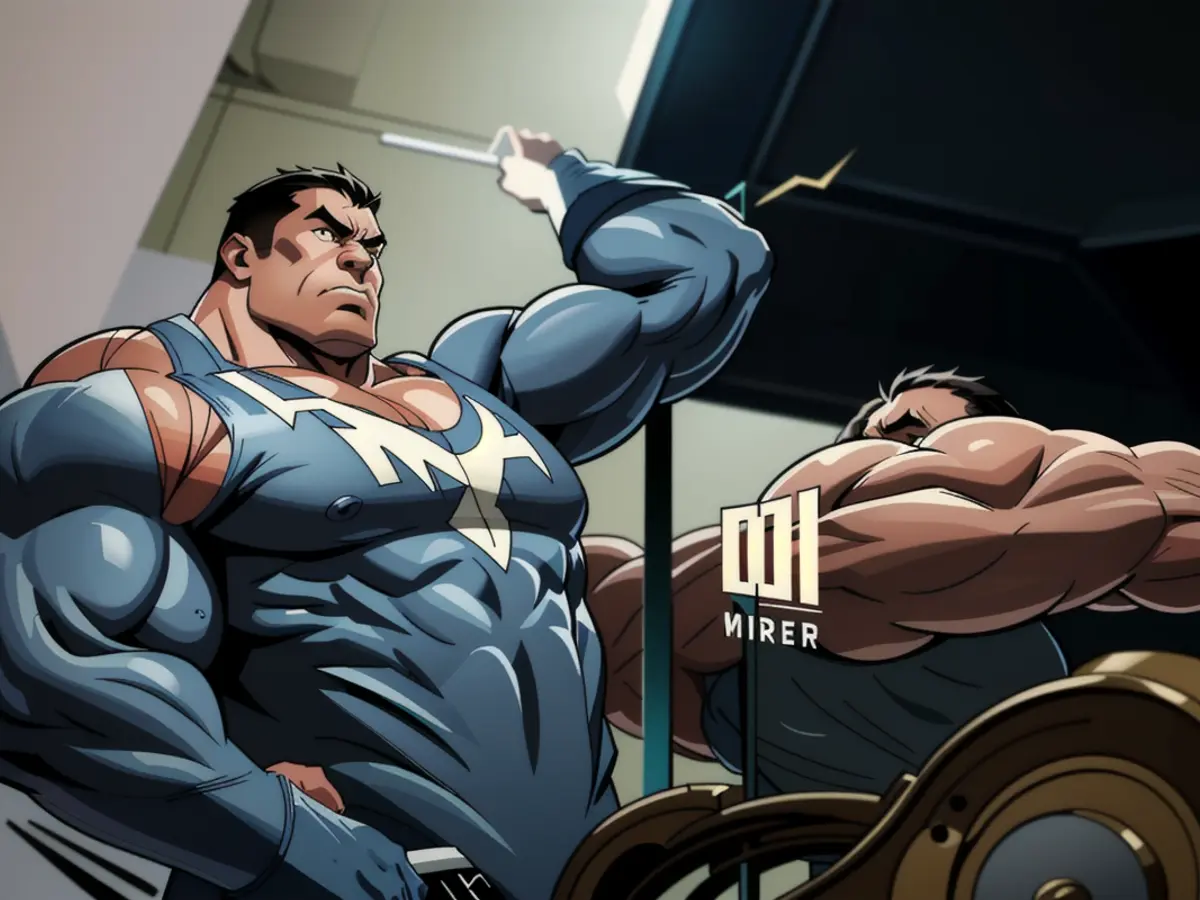
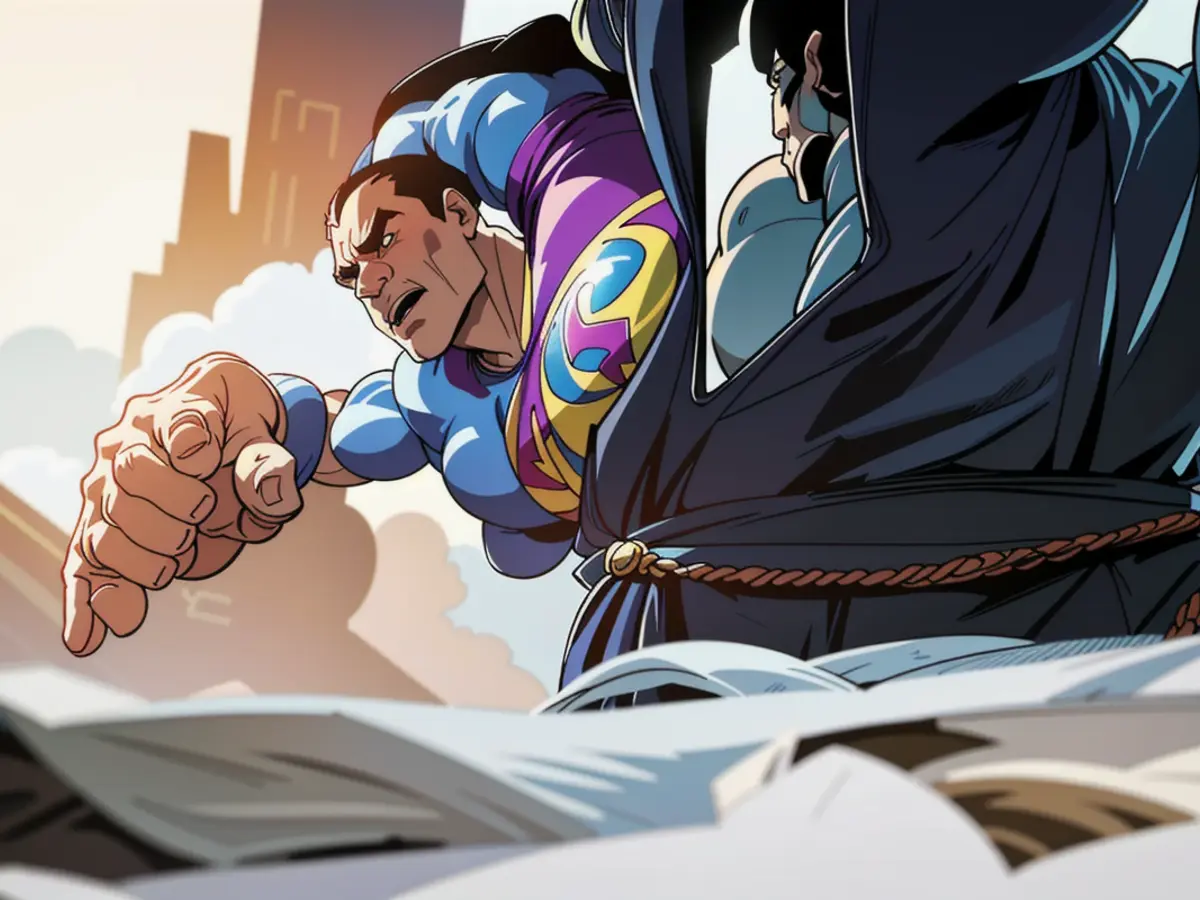